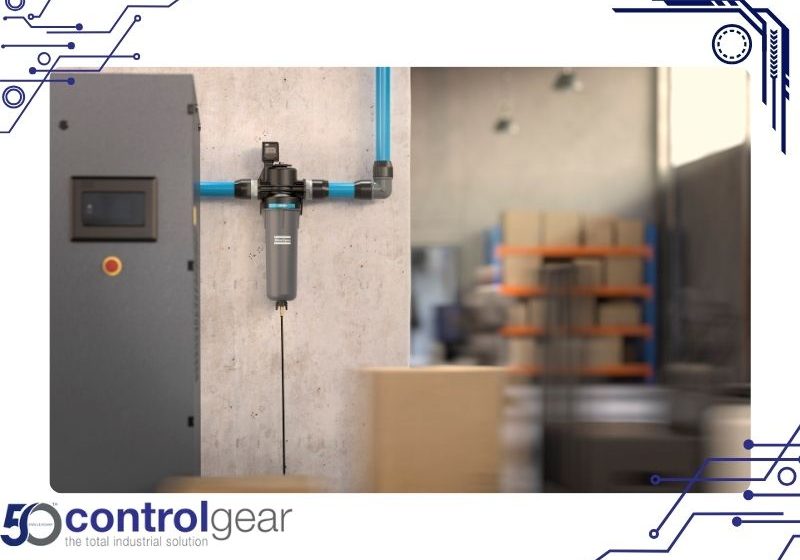
All You Need to Know About Compressed Air Quality Filters
Imagine contaminated air wreaking havoc on your production line – increased downtime, costly repairs, and compromised product quality. These are just some of the headaches caused by inadequate compressed air filtration.
Compressed air filters are your first line of defence against these problems, ensuring the air powering your operations is clean, dry, and safe. By removing harmful contaminants, quality filters protect your equipment, maintain product integrity, and contribute to a healthier, more efficient work environment.
This article explores the crucial role of high-quality compressed air filters, examining their types, applications, and the significant impact they have on your bottom line.
Why Compressed Air Filters are Important
Compressed air filters protect your compressed air system components from contaminants such as dust, oil vapours, and moisture. These impurities can damage the system without proper filtration, leading to costly repairs, reduced efficiency, and product defects.
Protecting Equipment and Reducing Downtime
Air compressor filters safeguard air-powered equipment from wear caused by solid and liquid contaminants, preventing unexpected breakdowns and expensive downtime. This ensures smooth operations, extends service life, and lowers maintenance costs.
Enhancing Product Quality
Unfiltered air can lead to contamination in industries with stringent air purity standards, such as food, pharmaceuticals, and electronics. For example, Class 0 certified oil-free compressors paired with high-efficiency filters ensure ISO 8573-1 compliance, safeguarding sensitive manufacturing environments. High-quality filters designed to remove impurities ensure product quality and compliance with purity classes such as ISO 8573-1.
Boosting Energy Efficiency
Efficient filters help maintain lower pressure drops, reduce compressor strain, and minimise energy waste. This improves overall system performance and lowers operating costs.
Compliance with Industry Standards
Filters meeting ISO standards, such as ISO 12500, help businesses comply with compressed air purity requirements, ensuring safety and efficiency. In sectors like medical or electronics, ISO-compliant filtration guarantees product reliability and adherence to regulations.
Key Features and Specifications for Air Quality
Selecting the right compressed air filter isn’t a one-size-fits-all approach. It requires understanding key technical specifications to match filter capabilities with your specific needs and industry standards.
Filtration Efficiency: The Gold Standard for Purity
Filtration efficiency refers to the filter’s ability to capture and remove contaminants from the compressed air stream. It’s typically expressed as a percentage, representing the proportion of particles of a specific size that the filter can trap.
- High-efficiency filters can remove up to 99.9999% of contaminants, ensuring exceptional air purity for even the most sensitive applications. Multistage filters combining coalescing, particulate, and activated carbon media are particularly effective. These filters often utilise multiple filtration stages and advanced media to capture a wide range of particle sizes.
Flow Rate: Matching Capacity with Demand
Flow rate is the volume of compressed air that can pass through the filter per unit of time, usually measured in cubic feet per minute (CFM). Choosing a filter with an inadequate flow rate can restrict airflow, leading to pressure drops and hindering system performance.
An undersized filter risks bottlenecks, while an oversized one increases energy costs. Regular audits help optimise flow rate alignment with system demands.
- Filter flow rate should always meet or exceed your system’s maximum air consumption demands. Consider future expansion plans when determining the appropriate flow rate to avoid bottlenecks.
ISO Standards: The Benchmark for Air Purity
The International Organization for Standardization (ISO) sets globally recognized standards for compressed air purity, classifying air quality into different classes based on particle size and concentration.
- ISO 8573-1: This widely used standard classifies compressed air purity based on particle size, water content, and oil content. Achieving Class 1 for particle filtration often necessitates advanced HEPA-grade filters and precision housing. Different classes within this standard, such as Class 1 or Class 2, define specific limits for each contaminant type.
When selecting air filters, ensure they clearly state their compliance with relevant ISO standards. This compliance provides assurance that the filter meets the necessary criteria to achieve your desired air purity level. For instance, a filter compliant with ISO 8573-1 Class 1 for particle filtration will guarantee a specific level of particle removal efficiency, ensuring air quality suitable for critical applications.
Benefits of Using High-Quality Compressed Air Filters
Investing in high-quality compressed air filters is not just an expense; it’s a strategic decision that yields significant returns in terms of operational efficiency, cost savings, and product quality.
Reduced Maintenance Costs: Preventing Problems Before They Arise
Contaminants in compressed air are a leading cause of equipment wear and tear. Particles can erode internal components, clog orifices, and damage seals, leading to costly repairs and downtime.
- Case Study: A manufacturing plant using lower-grade filters experiences frequent pneumatic tool failures due to particle contamination. After upgrading to high-efficiency filters, their tool maintenance costs decrease by 40%, and downtime drops by 20% within a year.
Extended Equipment Life: Protecting Your Investments
By removing abrasive particles and moisture, quality air filters protect your investments in expensive compressors, valves, cylinders, and other pneumatic equipment.
- Example: A compressor supplied with clean, dry air through effective filtration operates optimally for its intended lifespan, avoiding corrosion-induced failures and maximising ROI. This corrosion can lead to premature failure, requiring costly replacement. In contrast, a compressor supplied with clean, dry air through effective filtration can operate optimally for its intended lifespan, maximising your return on investment.
Improved Product Quality: Meeting Stringent Standards
In industries like food and beverage, pharmaceuticals, and electronics, compressed air purity is paramount to prevent product contamination.
- Example: In a pharmaceutical packaging facility, even microscopic oil aerosols in the compressed air used for product handling could lead to batch rejection and production delays. Installing ISO 8573-1 Class 1 compliant filters ensures safe operations and maintains stringent quality standards.
Enhanced Operational Efficiency: Minimising Downtime and Waste
Clean compressed air contributes to smoother, more efficient operations by preventing issues that lead to downtime, production bottlenecks, and product defects.
- Example: Printing companies often experience inconsistent ink application due to fluctuating air pressure caused by a clogged filter in their system. Upgrading to filters with lower differential pressure and higher dirt-holding capacity can reduce material waste and increase operational uptime by 30%.
By investing in high-quality compressed air filters, businesses can proactively address these challenges, achieving significant cost savings, improved product quality, and a more efficient, reliable production environment.
Types of Compressed Air Filters
Control Gear offers a variety of compressed air filters, suitable for diverse industrial needs:
Particulate Filters
These filters remove atmospheric dirt and solid particulates, providing up to 99.9999% particle removal efficiency. A typical application of a particulate filter is in the food and beverage industry, where absolute air purity is essential.
Typical application: in the food and beverage industry, particulate filters prevent contamination during critical production stages, such as bottling and packaging.
Particulate Filter Technical Data
- Atlas Copco particulate filters are typically available in three primary micron sizes: 3 micron, 1 micron, and 0.01 micron.
- Correct sizing ensures the filter catches even the smallest particles.
- Designed with high-performance borosilicate microfibres and treated with a water-repelling oleophobic agent to increase their efficiency and longevity.
- Capable of handling various flow rates, from 1 CFM (Cubic Feet per Minute) to a robust 5,000 CFM, allowing them to cater to a wide range of industrial applications.
- Micron sizes: Available in 3, 1, and 0.01 micron options.
- Material: Designed with borosilicate microfibres treated with an oleophobic agent for enhanced durability and efficiency.
- Capacity: Handles airflow rates from 1 CFM to 5,000 CFM.
- Updated feature: New hydrophobic coatings now allow operation in environments with up to 95% humidity without loss in filtration performance.
The particulate count largely depends on the size of the filter and the air quality in the working environment. However, with a filtration efficiency of 99.9999%, you can rest assured that the count of remaining particles post-filtration is minuscule.
Micro-biological Filters
These filters provide absolute removal of solid particulates and micro-organisms. Their stainless steel construction allows sterilisation using steam in situ. Pharmaceutical and healthcare industries, where sterilisation is critical, commonly use these filters.
Microbiological Filter Technical Data
- Atlas Copco micro-biological filters are renowned for their superior filtration capability.
- Available in two primary micron sizes, 0.01 micron and 0.003 micron, which makes them perfect for catching tiny micro-organisms as well as solid particulates.
- Manufactured from robust, high-grade 316L stainless steel to resist corrosion and withstand challenging operating conditions.
- Compliant with the stringent standards of the pharmaceutical and healthcare industries, where contamination risk must be minimal.
- A virtually negligible count of remaining particles post-filtration, assuring maximum hygiene and cleanliness.
- Can handle different flow rates, ranging from 1 CFM up to a substantial 5,000 CFM. This versatility allows the filters to cater to a wide spectrum of industrial applications.
- Enhanced feature: Filters now offer thermal resistance up to 180°C, increasing longevity during high-temperature sterilisation cycles.
Activated Carbon Filters
Activated carbon filters remove oil vapours and odours, ensuring uncontaminated final products.
New Application: these filters are now integrated into medical-grade oxygen production systems to maintain odourless oxygen streams.
Activated Carbon Filter Technical Data
- Atlas Copco’s activated carbon filters come in various sizes to accommodate different industrial needs. The filters can handle particulate sizes as small as 0.01 microns, providing a highly efficient filtration solution.
- The construction of these filters is top-notch, using durable and highly absorbent activated carbon.
- The activated carbon bed can adsorb up to 99.9999% of oil vapours, ensuring almost no contamination in the final product.
- These filters offer a high flow rate too, supporting capacities from 1 CFM to 5,000 CFM.
- Improvement: enhanced drainage mechanisms now allow 20% faster removal of collected liquid, reducing maintenance intervals.
With such exceptional technical specifications, Atlas Copco’s activated carbon filters are truly a benchmark for guaranteeing optimal air quality, in various industrial environments.
Coalescing Air Filters
These filters specialise in trapping and removing small liquid oil droplets and oil aerosols, which can harm equipment and product quality.
The filter operates by causing tiny droplets to coalesce, or come together, forming larger droplets that can be more easily drained away. These filters are particularly beneficial in industries that require dry, clean air, such as the automotive, electronics, and textile sectors.
Coalescing filters ensure a high level of air purity, ultimately reducing maintenance costs and enhancing overall operational efficiency.
Coalescing Filter Technical Data
- Atlas Copco’s coalescing filters cater to particulate sizes as minute as 0.01 microns, ensuring superior filtration.
- The material composition involves high-quality borosilicate microfibers, which offer impressive durability and efficient coalescing characteristics.
- These filters can handle high particulate counts, ensuring clean, dry air all the time.
- The flow rate is equally impressive, with capacities ranging from 1 CFM to 5,000 CFM.
Atlas Copco’s coalescing filters are a testament to the brand’s commitment to delivering high-quality, reliable, and efficient filtration solutions.
Dust Removal Filters
These filters efficiently remove dry particulates like dust, pollen, and mould spores, ensuring clean and breathable air. They trap these particles in a complex web of fibres, where the dust remains until the filter is either cleaned or replaced.
Dust removal filters are integral in industries that produce a significant amount of dust or where clean air is paramount, such as woodworking, metalworking, and pharmaceutical manufacturing.
Dust Removal Filter Technical Data
- Atlas Copco’s dust removal filters not only enhance the lifespan and reliability of your equipment, but also maintain a safe and healthy working environment.
- These filters tackle particle sizes as small as 1 micron, capturing fine dust and other particulates with ease.
- Manufactured from a unique blend of polyester and cellulose, ensuring excellent durability and dust capture rates.
- Can handle air flow rates ranging from 1 CFM to 5000 CFM, depending on the specific model.
- Updated design: redesigned pleated elements now provide 30% higher dust-holding capacity without increasing filter size.
These specifications underscore Atlas Copco’s relentless pursuit of excellence in producing high-performance, reliable filtration solutions.
Micro-biological Filters
Also known as membrane filters, these are designed specifically to remove or reduce microorganisms like bacteria, viruses, and fungi from the air stream. Operating under the principle of physical sieving and interception, they have a complex pore structure that allows air to pass through, while retaining the micro-organisms.
Technical Specifications of Micro-Biological Filters
- Atlas Copco’s micro-biological filters incorporate a superior design backed by rigorous performance data.
- Can filter particulates as small as 0.01 micron, offering a high degree of air purity.
- Constructed from durable materials like polyethersulfone, polyvinylidene fluoride, or nylon which provide excellent resistance against thermal and chemical impacts.
- Premium materials contribute to the filters’ long lifespan, reducing the need for frequent replacements.
- Maximum operating pressure of 16 bar (232 psi), ensuring filters can withstand high-pressure environments.
- Capable of handling very high particulate counts, with a standard particulate removal rate of 99.9999% at 0.01 microns, ideal for even the most demanding industrial applications.
- Update: Advanced sealing technology now improves microbial capture by 10%, ensuring even higher air purity levels.
Atlas Copco’s micro-biological filters maintain the highest level of air purity, safeguarding the quality and safety of end products.
Choosing the Right Air Quality Filter for Your Needs
Selecting the right compressed air filter isn’t about finding the most expensive option; it’s about finding the optimal solution for your specific operational environment and industry demands. Here’s a guide to help you make an informed decision:
Understanding Your Industry and Application
Different industries have vastly different compressed air quality requirements. Consider the specific needs of your sector:
Pharmaceuticals & Food Processing: These industries demand the highest level of air purity to prevent contamination. Look for filters with:
- Ultra-fine filtration capabilities: Capable of removing particles down to 0.01 microns or smaller, suitable for ISO 8573-1 Class 1 compliance.
- Sterile filtration options: Filters validated for sterile air applications with high-temperature resistance for steam sterilisation.
Electronics Manufacturing: Preventing electrostatic discharge (ESD) and ensuring particle-free air is crucial in this sector:
- Anti-static filters: Equipped with conductive housings to eliminate static buildup and ensure safe operations near sensitive electronic components.
- High-efficiency particulate filters: Certified to capture sub-micron particles down to 0.01 microns, reducing the risk of circuit damage.
Heavy-Duty Industrial Environments: Applications involving heavy machinery, painting, or abrasive processes require robust filtration:
- Coalescing filters: Advanced designs that remove up to 99.9999% of oil aerosols and water vapour, extending equipment life.
- Dust removal filters: Filters designed to handle extreme dust loads with increased dirt-holding capacity, reducing replacement frequency.
Evaluating Operational Factors
Beyond your industry, consider these operational factors:
- Operating Environment: Is your facility in a high-humidity area? Do you generate significant dust or oil mist? Your environment will dictate the types of contaminants you need to filter and the filter’s required durability.
- High-humidity environments: Consider filters with advanced hydrophobic coatings to maintain performance even under wet conditions.
- Expected Particulate Load: The amount of dust, oil, and other contaminants present in your compressed air directly impacts filter lifespan. Higher particulate loads may require more frequent filter changes or a multi-stage filtration system.
- Recommendation: Multi-stage filtration systems for environments with high contaminant levels, optimising longevity and efficiency.
- Desired Purity Level: Clearly define your required air purity level based on your application and relevant ISO 8573-1 classifications. This will guide you towards filters that meet your specific purity needs.
- ISO Class 0 or Class 1 filters: Meet stringent standards for industries requiring oil-free compressed air.
By carefully considering your industry, application, and operating environment, and working closely with a reputable compressed air specialist, you can select the optimal air filter solution to maximise equipment protection, enhance product quality, and ensure the long-term efficiency of your compressed air system.
Anatomy of a Compressed Air Filter
A compressed air filter is made up of several key components, each essential for efficient compressed air treatment and maintaining high-quality compressed air.
Filter Element: The Core of Filtration
The filter element traps contaminants such as dust, oil aerosols, and moisture from the inlet air. High-efficiency materials, such as borosilicate microfibres or activated carbon, ensure effective filtration. A larger surface area increases the element’s capacity to handle a higher contaminant load, ensuring the delivery of pure compressed air and extending the filter’s service life.
- New materials: Filters now incorporate nano-fibre technology to enhance particle retention and reduce pressure drop.
- Larger surface area: Advanced pleating designs increase filtration capacity by up to 30%.
Filter Housing: Durable Protection
The filter housing encloses the element, protecting it from external conditions. Constructed from materials like stainless steel or aluminium, it resists wear and prevents leaks, even under the high pressures of the compressed air process. This ensures the filter operates effectively, maintaining the overall quality of compressed air.
- Enhanced durability: Constructed with reinforced stainless steel to withstand pressures of up to 25 bar.
Drain Valve: Managing Moisture
The drain valve at the bottom of the filter automatically removes water and oil, preventing corrosion and ensuring optimal filtration performance. Regular maintenance of the drain valve is essential for keeping the system running smoothly.
- Automatic zero-loss drain valves: These reduce maintenance and ensure energy-efficient operation.
End Caps and Seals
End caps secure the filter element, creating a tight seal that ensures all air passes through the system. This prevents unfiltered air from bypassing the element, guaranteeing the removal of contaminants and supporting clean, high-efficiency air.
- Improved sealing: Silicone-free seals now offer enhanced resistance to extreme temperatures and chemicals.
Flow Optimisation
Filters are designed with optimised flow paths to reduce differential pressure and maintain a low-pressure drop. This allows air to pass efficiently while minimising energy loss. Coalescing technology helps combine and remove water droplets and oil, ensuring clean air for downstream applications.
- Coalescing technology: Improved droplet coalescence ensures higher oil and water removal efficiency.
The Role of Water Separators
Water separators are essential to protect coalescing filters from bulk liquid contamination. They employ mechanical separation techniques and can remove over 92% of bulk liquid contamination, making them ideal in environments with high humidity levels.
Compressed air dryers are integral to the water separation process, working synergistically with water separators to ensure optimal performance and longevity.
- Updated design: advanced centrifugal separators now achieve 98% efficiency in removing bulk water, even at varying flow rates.
- Energy-saving dryers: Atlas Copco’s latest range features integrated dew-point sensors for adaptive performance, reducing energy consumption by up to 25%.
Compressed air dryers are an integral part of the water separation process, working synergistically with water separators to ensure the optimal performance, and longevity, of your equipment.
The core function of a compressed air dryer is to reduce the dew point of the air, effectively removing the water vapour present. Doing so ensures the air is dry before it reaches the water separator, increasing its efficiency and lifespan.
Atlas Copco offers a range of energy-efficient compressed air dryers that further enhance the efficiency of water separators. The dry, clean air produced not only protects tools and equipment, but also improves overall operational performance, by minimising downtime and maintenance costs.
Selecting the Right Compressed Air Filter
When choosing compressed air filtration products for equipment, consider factors including: the air quality required for your specific application, the overall cost of ownership, and the equipment’s environmental impact.
- Application-specific requirements: Match filter types to ISO classifications for optimal performance.
- Cost-efficiency: Avoid over-treatment of air by selecting filters aligned with your operational needs.
- Environmental impact: Use filters with recyclable components and minimal energy losses.
Avoid over-treating the air as it can lead to unnecessary costs without improving the air quality to a useful level. For example, using a high-cost sub-micro filter in an air compressor that only requires a general-purpose filter, will increase expenses without adding value to the process.
Lastly, always factor in long-term costs, including maintenance, repairs, and replacements. Atlas Copco filters, known for their robust construction and high filtration efficiency, tend to incur lower overall costs. Their longer filter life reduces the frequency of replacement, and their reliability ensures minimal repair costs, resulting in lower total cost of ownership.
Example: New Atlas Copco filters have a 20% lower lifecycle cost than competitors, thanks to extended filter life and reduced energy usage.
Always keep these factors in mind when selecting your compressed air filters. Similarly, consider long-term costs, such as repairs and replacements and buy air filters that provide maximum efficiency, while minimising maintenance expenses.
Maintaining Compressed Air Quality
Maintaining high-quality compressed air requires a proactive approach that extends beyond simply installing a filter and forgetting about it. Regular maintenance and timely replacement are essential to ensuring optimal system performance, prolonging equipment lifespan, and avoiding costly downtime.
Proper installation is the first step towards effective filtration. Ensure filters are installed according to manufacturer guidelines, paying close attention to factors like airflow direction, sealing surfaces, and proper pre-filtration stages. Even a slight deviation from recommended practices can compromise filtration efficiency, leading to bypass and premature clogging.
- Updated guidelines: Install pre-filters before coalescing filters to maximise efficiency and extend the lifespan of primary filters.
Routine maintenance is crucial to maximising filter lifespan and system performance. Regularly inspect filters for signs of clogging, such as increased pressure drop across the filter housing. Monitor pressure differentials and establish a replacement schedule based on manufacturer guidelines, operating hours, and observed pressure changes.
Tip: Use digital monitoring systems to track differential pressure in real time, ensuring timely replacements.
Key Takeaways – Compressed Air Quality Filters
The importance of selecting and maintaining quality air filters in your air compressor system cannot be overstated. Choosing the correct filter not only ensures the best performance, but it also prevents unnecessary costs, and contributes to a more sustainable industrial environment.
- Investment impact: High-quality filters can reduce downtime and energy costs by up to 40%.
Atlas Copco products stand out with their robust construction, high filtration efficiency, and minimal environmental impact. Remember, a wise investment in quality filters today can save you significant costs and hassles down the line.
Trust Control Gear to provide the reliability and efficiency you need in compressed air quality filters. Don’t compromise on the quality and performance of equipment. Get expert advice and help from the Control Gear team to select the perfect air filter for your air compressors.
Remember, choosing the right filter can make all the difference in maintaining the quality, efficiency, and longevity of your equipment. Experience the benefits of high-quality air filters with Control Gear and Atlas Copco today.
Frequently Asked Questions
1. What types of filters are best for achieving high-quality compressed air?
Compressed air systems benefit from a range of filters, including particulate filters, coalescing filters, and adsorption filters, each designed to remove specific contaminants. For high-quality compressed air, a combination of particulate and coalescing filters is recommended to remove solid particles, liquid water, and oil aerosols. Adsorption filters are ideal for capturing carbon particles and ensuring air purity. These filters are designed to remove impurities and meet purity standards such as ISO 8573-1.
2. How do I find the right filter for my compressed air system?
Finding the right filter depends on your application, system specifications, and air purity requirements. Consider the type of filter needed based on the contaminants in your air, such as dust, oil, or moisture. The filter’s adsorption capacity, pressure dew point, and large surface area should also align with your system’s demands. If you need more clarification, our team of experts can help you choose the optimal filter to maintain high efficiency and protect your equipment. Don’t hesitate to get in touch for personalised guidance.
3. Why is regular maintenance of compressed air filters important?
Regular maintenance ensures that your filter products perform at their best, consistently removing contaminants such as dust, oil, and water from the system. Over time, contaminants can clog filters, increasing differential pressure and reducing efficiency. Proper upkeep of line filters and screw compressors prevents pressure drops, protects your piping system, and helps maintain the purity of the air that is compressed, ensuring reliable performance and system longevity.